.jpg)
Disclaimer: Copyright infringement not intended.
Context
- Quality Control Orders (QCO) have been issued for fibers — cotton, polyester and viscose — that constitute the basic raw materials for the majority of the Indian textile and clothing industry.
Quality Control Orders (QCOs)
- For ensuring the availability of quality products to consumers, Quality Control Orders (QCOs) are issued by various Ministries/Departments of the Government of India in the exercise of the powers conferred by section 16 of the Bureau of Indian Standards Act, 2016 stipulating conformity of the products to Indian Standards.
Read all about BIS: https://www.iasgyan.in/daily-current-affairs/bureau-of-indian-standards-bis
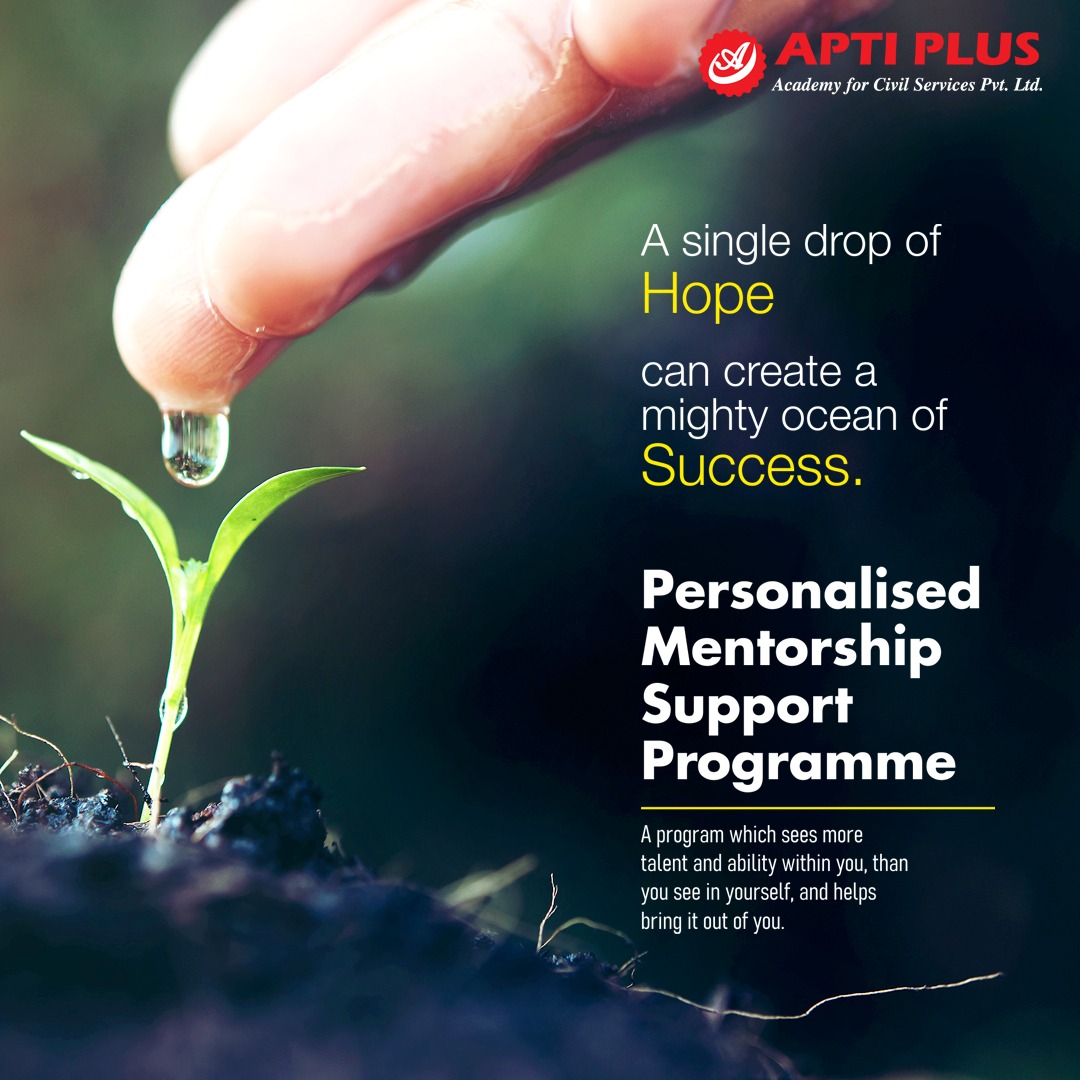
New Mandate-QCO issued for fibers: The recent move
- While the standards set by Quality Control Orders (QCO) were available earlier too, these are now revised and made mandatory for a few, and yet to be finalized for others.
- International manufacturers of these fibres, who supply to India, are also mandated to get a certificate from the Bureau of Indian Standards (BIS), which is the certifying authority for the QCOs.
Why are fibres covered under QCOs?
- The Indian textile and clothing industry consumes both indigenous and imported fibres and filaments.
- The imports are for different reasons — cost competitiveness, non-availability in the domestic market, or to meet a specified demand of the overseas buyer.
- The main aim of the QCO is to control import of sub-quality and cheaper items and to ensure that customers get quality products. The entire supply chain, from the textile manufacturers to exporters, has so far focused on quality standards prescribed by the buyers.
What challenges does the new mandate bring?
Costly affair+ Loss of Value Chain
- India imports annually 50,000 - 60,000 tonnes of viscose fibre and its variants such as Modal and Tencel LF from nearly 20 countries. In the case of polyester, almost 90,000 tonnes of polyester fibre and 1.25 lakh tonnes of POY (Polyester Partially Oriented Yarn) are imported annually.
- The overseas fibre manufacturers sell not only to India but to other countries too. The supply of some fibres to India is in small quantities. Getting the certificate from the BIS involves a cost and and hence not all are interested in getting the certificate.
- The Indian textile manufacturers who are dependent on these suppliers for the raw material will have to either look at other suppliers or lose orders.
Understanding through an example
- For instance, a bed linen exporter in Tiruppur district imports polyester filament with functional properties from Turkey based on the demand of his European buyers.
- Though the imported filament constitutes just 6% of the product, the buyer has specified the source for the filament.
- Since the Turkey company is not interested in getting the BIS certificate, the exporter in Tiruppur has lost an order to Pakistan. Furthermore, BIS officials have to visit the manufacturing unit abroad before issuing the certificate and this process is yet to be completed for all suppliers who have applied for the BIS registration.
- There is no clarity on the fibres that were shipped before the certification and which will reach India in the coming days.
- The textile buyers, be it domestic or international, have established a supply chain over the years and when there are constraints because of certification, the value chain is disrupted.
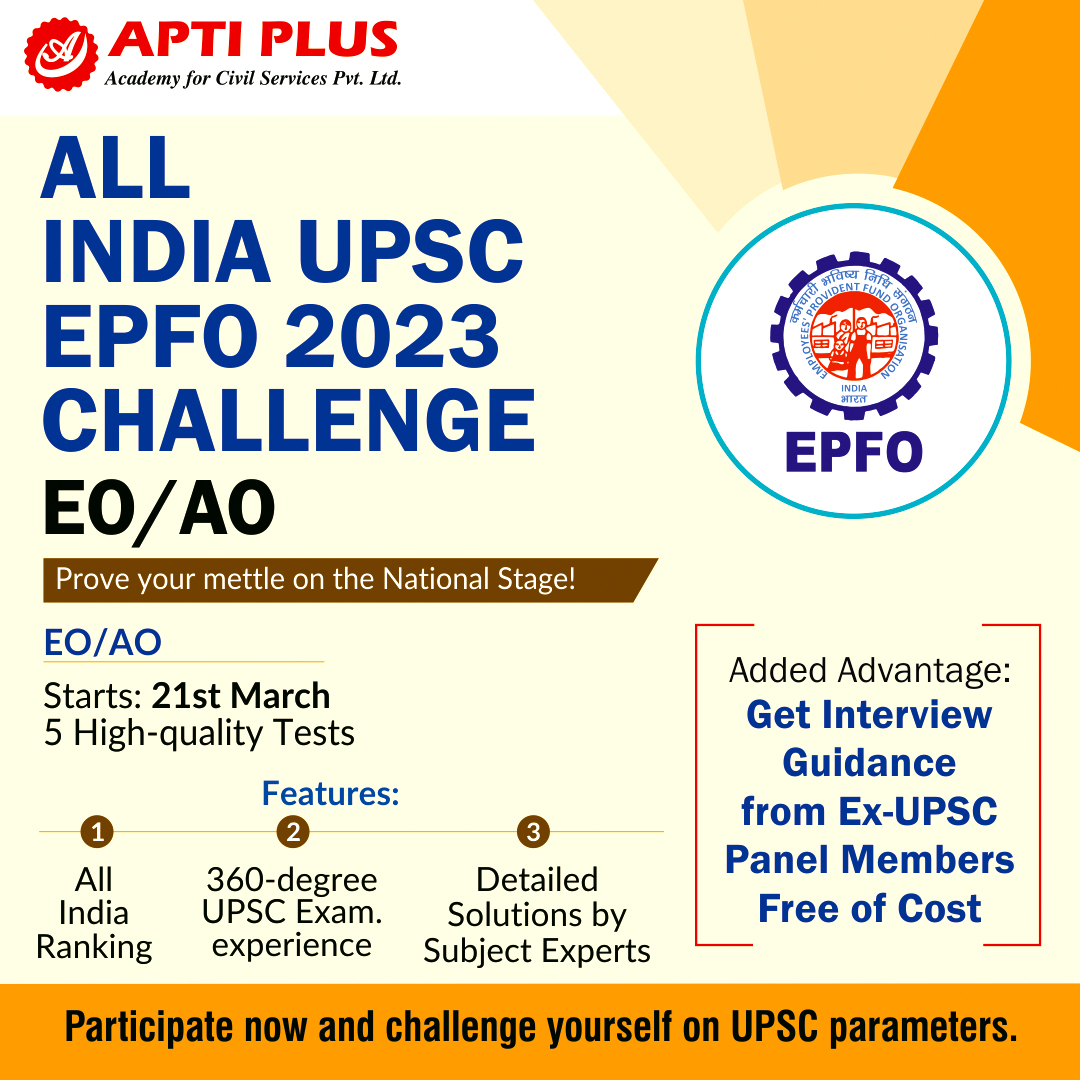
What is the Way Forward?
- Be it viscose or polyester, some varieties of the fibre have special functional properties and separate HS (Harmonised Commodity Description and Coding System) code when imported. But, these are bundled in the QCO and thus have uniform quality standards.
- The textile industry imports just small quantities of such fibres and restricting its availability will deny Indian consumers of niche products.
- The textile industry is of the view that import of speciality fibres that are used as blends with other fibres should be made available without restriction.
- Also, any overseas applicant for the BIS certificate should get it without delay after inspection.
- Several textile units use lower-grade fibres that are generated from rejects and wastes and these are not covered under the QCO.
- There is also a fear of costs going up for basic garments.
- Further, polyester spun yarn mills in the MSME sector need capital support to set up labs to test products.
- The QCO should be implemented only after the ambiguities are cleared and the anomalies set right, says the industry.
Note: The BIS standards are mandatory for viscose staple fibre from March 29 and for five polyester products, including polyester staple fibre and polyester spun yarn from April 3 2023.
Trivia
Harmonized System (HS)
- The Harmonized Commodity Description and Coding System, also known as the Harmonized System(HS) of tariff nomenclature is an internationally standardized system of names and numbers to classify traded products.
- It came into effect in 1988 and has since been developed and maintained by the World Customs Organization(WCO) an independent intergovernmental organization based in Brussels, Belgium, with over 200 member countries.
- HS Code is used by customs authorities around the world to identify products when assessing duties and taxes and for gathering statistics.
- The HS is administrated by the World Customs Organization(WCO) and is updated every five years.
Code Structure
- The HS code consists of 6-digits.
- The first two digits designate the HS Chapter.
- The second two digits designate the HS heading.
- The third two digits designate the HS subheading.
HS code 1006.30, for example indicates Chapter 10 (Cereals), Heading 06 (Rice), and Subheading 30 (Semi-milled or wholly milled rice, whether or not polished or glazed).
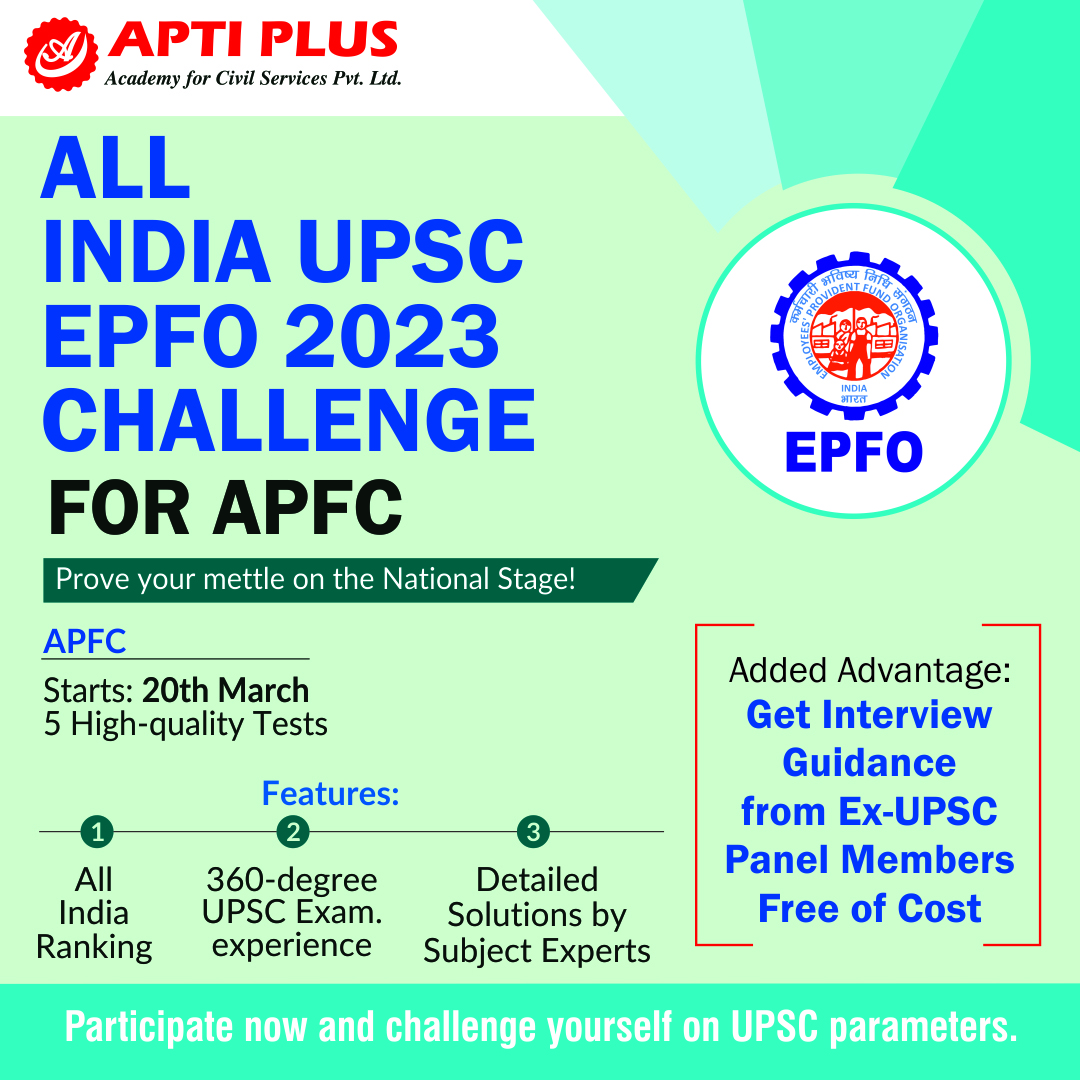
Other Steps taken by the Government to improve Quality Standards of products
The Government of India has taken a number of steps to improve the quality standards of products manufactured.
Standard mark (ISI mark):
- BIS grants licence to manufacturers to use the Standard mark (ISI mark) on the product conforming to the relevant Indian Standards.
Production-Linked Incentive (PLI) Scheme:
- To provide a major boost to manufacturing, the government has launched Production-Linked Incentive (PLI) Scheme for 13 sectors.
Public Procurement Order:
- In order to provide purchase preference to domestic manufacturers, Public procurement (Preference to Make in India) Order on Industrial Steam generators/ Boilers has been issued.
Identification of focus sub- sectors:
- 24 focus sub- sectors have been identified under Make in India 2.0 to enhance competitiveness and exports of the manufacturing sector.
Empowered Group of Secretaries (EGoS) and Project Development Cells (PDCs):
- Government has set up Empowered Group of Secretaries (EGoS) and Project Development Cells (PDCs)in Ministries/Departments to fast-track investments by coordination between the Central Government and State Governments
Udyog Manthan:
- First of its kind brainstorming exercise to enhance productivity & quality in Indian industry to realize vision of an AatmaNirbhar Bharat for all major sectors of manufacturing and services
Strengthening of IPR Regime:
- Infrastructure upgradation, digitisation of workflow in IP offices, manpower augmentation; Bolstering IP protection for MSMEs and Start-ups through dedicated schemes
New definition of MSME:
- The definition of micro manufacturing and services unit increased to Rs. 1 crore of investment and Rs. 5 crore of turnover.
- The limit of small unit increased to Rs. 10 crore of investment and Rs 50 crore of turnover.
- Similarly, the limit of a medium unit increased to Rs 20 crore of investment and Rs. 100 crore of turnover.
- The limit for medium manufacturing and service units was further increased to Rs. 50 crore of investment and Rs. 250 crore of turnover.
- It has also been decided that the turnover with respect to exports will not be counted in the limits of turnover for any category of MSME units whether micro, small or medium.
Read about Quality Council of India: https://www.iasgyan.in/daily-current-affairs/quality-control-of-india-14
PRACTICE QUESTION
Q. A quality control system based on a recognized standard, provides a strong foundation for achieving a wide range of marketing and operational benefits. What steps have been taken by the Government to improve Quality Standards of products in India? Explain.
|
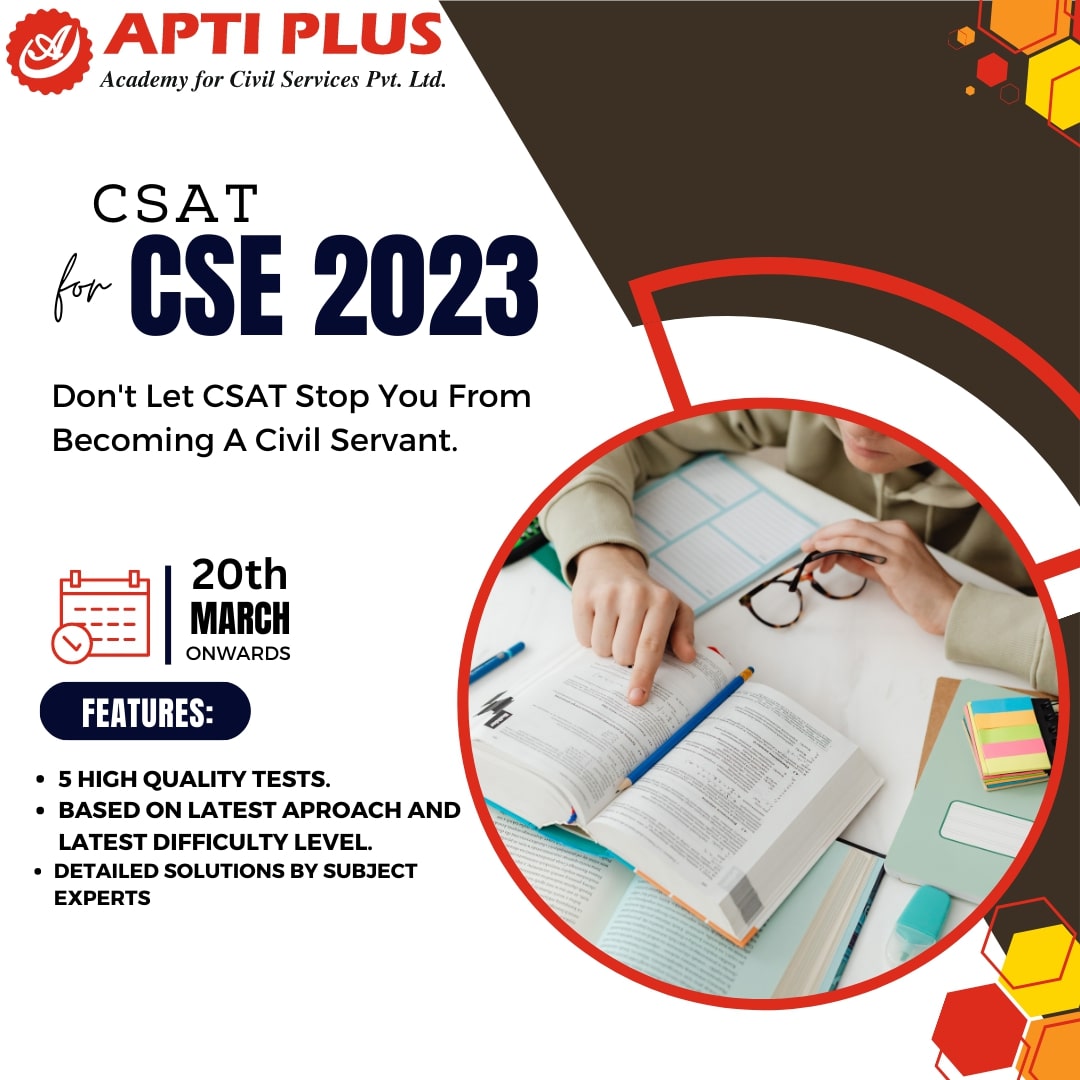
https://www.thehindu.com/business/Economy/explained-what-are-the-issues-with-the-new-quality-control-orders-for-fibres/article66681081.ece